Albasense
Microwave Plasma Assisted Sputter (MPAS)
System
Albasense Ltd provides customized, reliable microwave plasma assisted sputter (MPAS) deposition systems for optical applications

MPAS Technology
-Microwaves (2.42GHz) have higher ionization efficiency than RF (13.56MHz) for a given plasma, particularly at low pressures, where the plasma conductivity is lower.
- Because of a lack of electrodes, the probability of contamination and damage for sensitive applications are significantly reduced, alongside a near maintainence-free approach.
- Lower ion energies can reduce damage in wafer processing. Oscillation amplitude for electrons in microwave plasmas is about 10_100 microns, so both electron loss and plasma potentials are much lower than in RF discharges.
- Resulting benefits for optical coatings are reduced stress, increased film packing density (minimized environmentally reduced spectral drift) and lowered optical absorption
- Microwave plasma effectively pre-conditions the chamber prior to deposition in relation to removal of water which is particularly important for deposition of infrared coatings Surface Wave Microwave Plasma delivery via a directional coupler ensures plasma uniformity across the rotating drum and separated deposition and reaction zones enables independent optimisation of deposition & plasma assist
Benefits
• MPAS provides room temperature deposition
• Multi-sputter targets provides means to separately deposit adhesion promoting coatings, single material coating deposition and/ or co-deposition of two different coatings materials including metals and/ or oxides .
• Separate deposition & microwave plasma processing regions provide use of microwave plasma for effective pre-preparation of deposition chamber (esp. water vapor removal which can disrupt coating processes) and substrate microwave plasma pre-clean prior to deposition
• Control system provides single layer or multilayer deposition.
• Optical gas control – plasma emission spectroscopy for reactive deposition processes
• Flexibility in coating stoichiometric control through variation in microwave plasma conditions and gas composition, nanostructural modification & control through combination of microwave plasma/ pulsed DC/ plasma control
• Optional MPAS co-deposition providing simultaneous deposition of two or more materials resulting in mixed and/ or graded materials
• Optional MPAS hydrogenated processes provide method for material bandgap modification [eg silicon bandedge]
• Drum floats electrically and ion energy can be controlled by gas flow and/ or separately applied bias if required
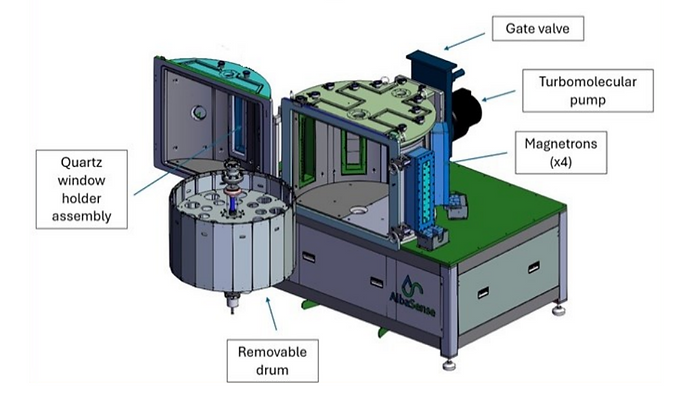